Pneumatic chamber pump “Beaver”
- Pneumatic chamber pumps of the new generation “Beaver”
- Supply of equipment and components
- Pneumatic transport lines and systems
- Equipment and facilities for receiving, storing and issuing material
Pneumatic chamber pump of the new generation "Beaver"
The Beaver pneumatic chamber pump belongs to a new generation of chamber pumps and is designed for pneumatic transport of bulk material in a dense layer with an average speed of 2÷3 m/s through pipelines from 50 to 300 mm in diameter.
Calculation of pneumatic transport:
The transportation performance depends on the volume of the pump chamber and ranges from 5 to 600 t/h. The capacity of a chamber pump for a specific task can be from 0.2 to 60 m3. Pumps can be sequentially connected to a pneumatic transport line every 200-300 meters for transportation over long (any) distances.
WithAt the same time, the consumption of compressed air will be 12-16 nm3 of atmospheric air (0.50-1.125 kWh of electricity) per ton of material in each pump.
“Beaver” chamber pumps for the first time actually transport bulk materials in a “dense layer” at a density of the transported material pulp of 0.6-0.9 t/m3.
This makes it possible to use pneumatic transport where it was not used before.
Technical characteristics of the “Beaver” pump
Main characteristics | Characteristic | units | 300B | 500B | 1000B | 1500B | 3000B | 5000B | 10000B | 15000B | 20000B |
The volume of the pump chamber | m3 | 0,3 | 0,5 | 1 | 1,5 | 3 | 5 | 10 | 15 | 20 | |
Productivity* (at a density of 1000 kg/m3) | t/h | 5 | 10 | 25 | 40 | 60 | 85 | 115 | 160 | 200 | |
Transport distance* | m | 50 | 80 | 90 | 100 | 120 | 180+ | 200+ | 200+ | 200+ | |
The maximum lifting height for material with a density of 1000 kg/m3 | m | 15 | 20 | 25 | 30 | 30 | 30 | 40 | 40 | 40 | |
Standard working pressure of the pump (SRDN) | MPa | 0,15-0,3 | 0,15-0,4 | 0,15-0,4 | 0,15-0,5 | 0,2-0,5 | 0,3-0,6 | 0,3-0,7 | 0,3-0,7 | 0,3-0,7 | |
Specific normalized air consumption at SRDN | Nm3/t | 4-8 | 6-10 | 6-10 | 6-12 | 8-12 | 12-15 | 16-24 | 16-24 | 16-24 | |
Average specific consumption of compressed air | m3/t | 2,4 | 2,5 | 2,6 | 2,6 | 2,6 | 2,6 | 2,8 | 2,8 | 2,8 | |
Average air flow | Nm3/min | 0,5 | 1,4 | 3,5 | 6 | 10 | 20 | 40 | 54 | 67 | |
Average specific consumption of electricity | kW-hr/t | 0,54 | 0,72 | 0,72 | 0,81 | 0,9 | 1,22 | 1,8 | 1,8 | 1,8 | |
Average energy consumption | kW-hr | 2,7 | 7,2 | 18 | 32,4 | 54 | 103,7 | 207 | 288 | 360 | |
Diameter of the transport main, from | mm | 60 | 80 | 100 | 100 | 150 | 150 | 200 | 200 | 200 | |
Pump diameter | mm | 750 | 950 | 1250 | 1450 | 1850 | 1850 | 2050 | 2450 | 2450 | |
Pump height, max. | mm | 1050 | 1450 | 1650 | 2050 | 2300 | 2800 | 3400 | 4250 | 5200 | |
Maximum mass | kg | 400 | 600 | 1150 | 1250 | 2000 | 2500 | 3300 | 4000 | 5400 |
*The range, height of transport and performance of the pump depends on specific conditions and requirements. Range and height can be increased by reducing productivity and vice versa, productivity can be increased by reducing the length of the transporting pipeline.
Complete set of Beaver “Standard” | Components | Units | 300B | 500B | 1000B | 1500B | 3000B | 5000B | 10000B | 15000B | 20000B |
Sliding shutter D 100 mm | pc | 1 | 1 | 1 | – | – | – | – | – | – | |
Sliding shutter D 150 mm | pc | 1 | 1 | – | 1 | 1 | 1 | – | – | – | |
Sliding shutter D 200 mm | pc | – | – | 1 | – | – | – | 1 | 1 | 1 | |
Sliding shutter D 300 mm | pc | – | – | – | 1 | 1 | 1 | – | – | – | |
Gate valve DN 400 mm | pc | – | – | – | – | – | – | 1 | 1 | 1 | |
Disc rotary shutter D 50 mm | pc | 1 | 1 | 1 | 1 | – | – | – | – | – | |
Disc rotary shutter, diameter 80 mm | pc | – | – | – | – | 1 | 1 | – | – | – | |
Disc rotary shutter D 100 mm | pc | – | – | – | – | – | – | 1 | 1 | 1 | |
Disc rotary shutter D 150 mm | pc | 1 | 1 | – | – | – | – | – | – | – | |
Disc rotary shutter D 200 mm | pc | – | – | 1 | – | – | – | – | – | – | |
Disc rotary shutter D 300 mm | pc | – | – | – | 1 | 1 | 1 | – | – | – | |
Disc rotary shutter D 400 mm | pc | – | – | – | – | – | – | 1 | 1 | 1 | |
Limit level alarm | pc | 1 | 1 | 1 | 1 | 1 | 1 | 1 | 1 | 1 | |
Pressure transducer | pc | 1 | 1 | 1 | 1 | 1 | 1 | 1 | 1 | 1 | |
Adjustable safety valve | pc | 1 | 1 | 1 | 1 | 1 | 1 | 1 | 1 | 1 | |
Microwave motion sensor | pc | – | – | – | – | – | – | 1 | 1 | 1 |
* Installation of sliding or disk rotary shutter
EBRO-Armaturen; Xurox; CMO; Genebre
Control cabinets | Characteristic | Units | 300B | 500B | 1000B | 1500B | 3000B | 5000B | 10000B | 15000B | 20000B |
BPU 20 pneumatic control unit | pc | 1 | 1 | – | – | – | – | – | – | – | |
BPU 50 pneumatic control unit | pc | – | – | 1 | 1 | – | – | – | – | – | |
BPU 80 pneumatic control unit | pc | – | – | – | – | 1 | 1 | – | – | – | |
BPU 100 pneumatic control unit | pc | – | – | – | – | – | – | 1 | 1 | 1 | |
Automation cabinet per set. “ARIES” or “SIEMENS” | pc | 1 | 1 | 1 | 1 | 1 | 1 | 1 | 1 | 1 |
The main competitive advantages of the pneumatic conveying system pumps “Beaver», working on the basis of the principle“Pneumatic equipment technologies”
The pneumatic chamber pump and the equipment included in the line should be considered not as separate objects, but as a single “pneumatic transport system”, which includes both the pump itself and the transport main with all its elements and nodes that have , sometimes, of decisive importance in the process of pneumatic transport of material. The fundamental difference between this pneumatic transport system and others similar in name is the method of moving the material in the pipe. Beaver pneumatic chamber pumps move the material through the pipein a dense layer with a speed of 1-3 m/s, depending on the material. The implementation of this process, in comparison with other ways of moving loose materials, entails a number of serious advantages, including:
- Many times reduced air flow, more than 5 times, on the transportation of material in comparison with similar methods of pneumatic transport, as a resultsavings on energy consumption and high profitability depending on performance.
- The possibility of using compressor equipment with low productivity.
- Abrasive impact reduced to a minimum on elements and nodes of the pipeline (hundreds of times compared to jet pneumatic transport), there is no need to purchase “abrasion-resistant leads”, as a result, a very high rate of preservation of the physical and mechanical properties of the material after the end of the transportation process.
The reliability of the entire pneumatic transport system has increased, including due to a reduction in the speed of movement of material in the pipe by tens or even hundreds of times, and, as a rule, an increased service life of the equipment for wear.
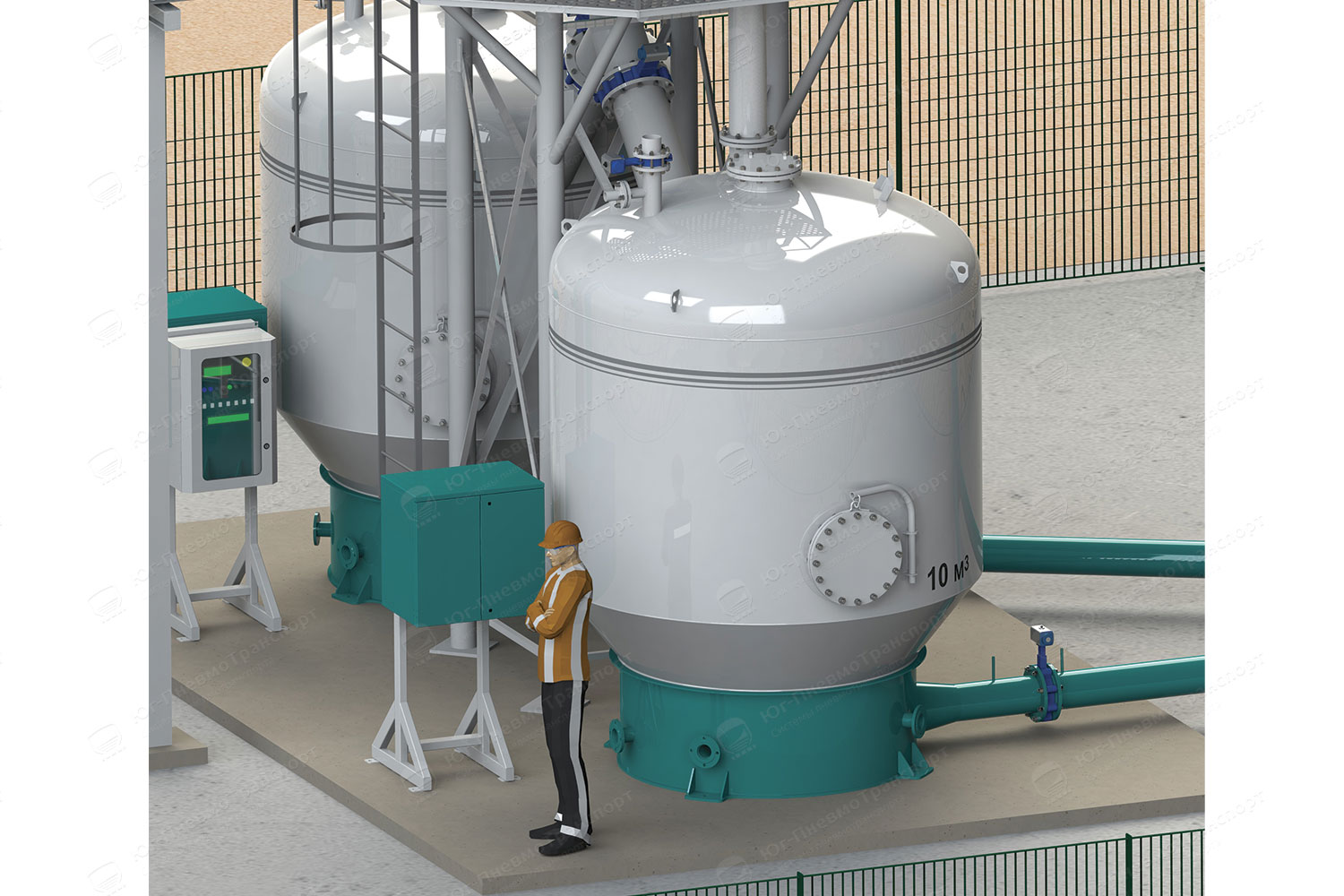